Example Robotic Welder Pictures
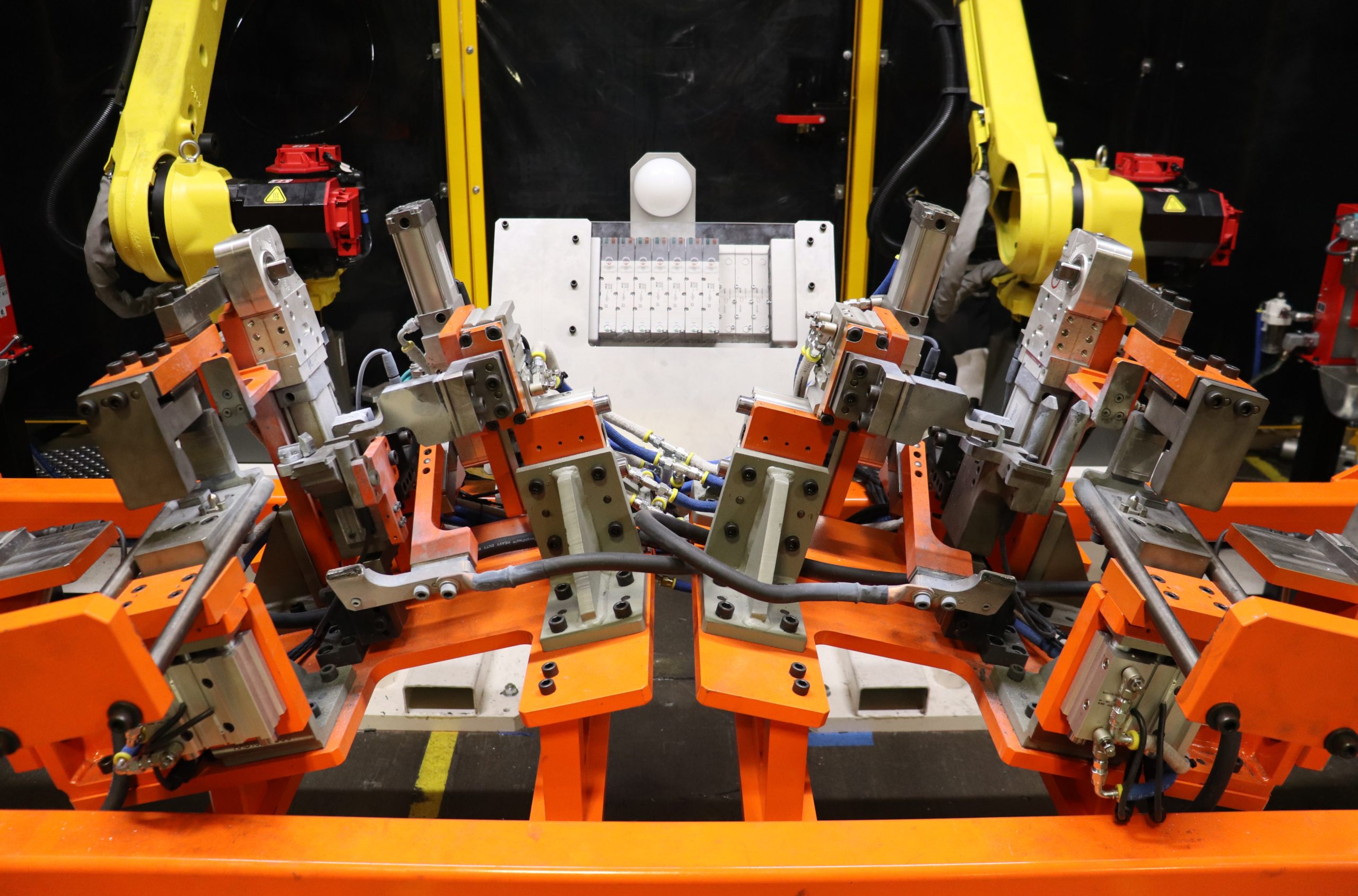
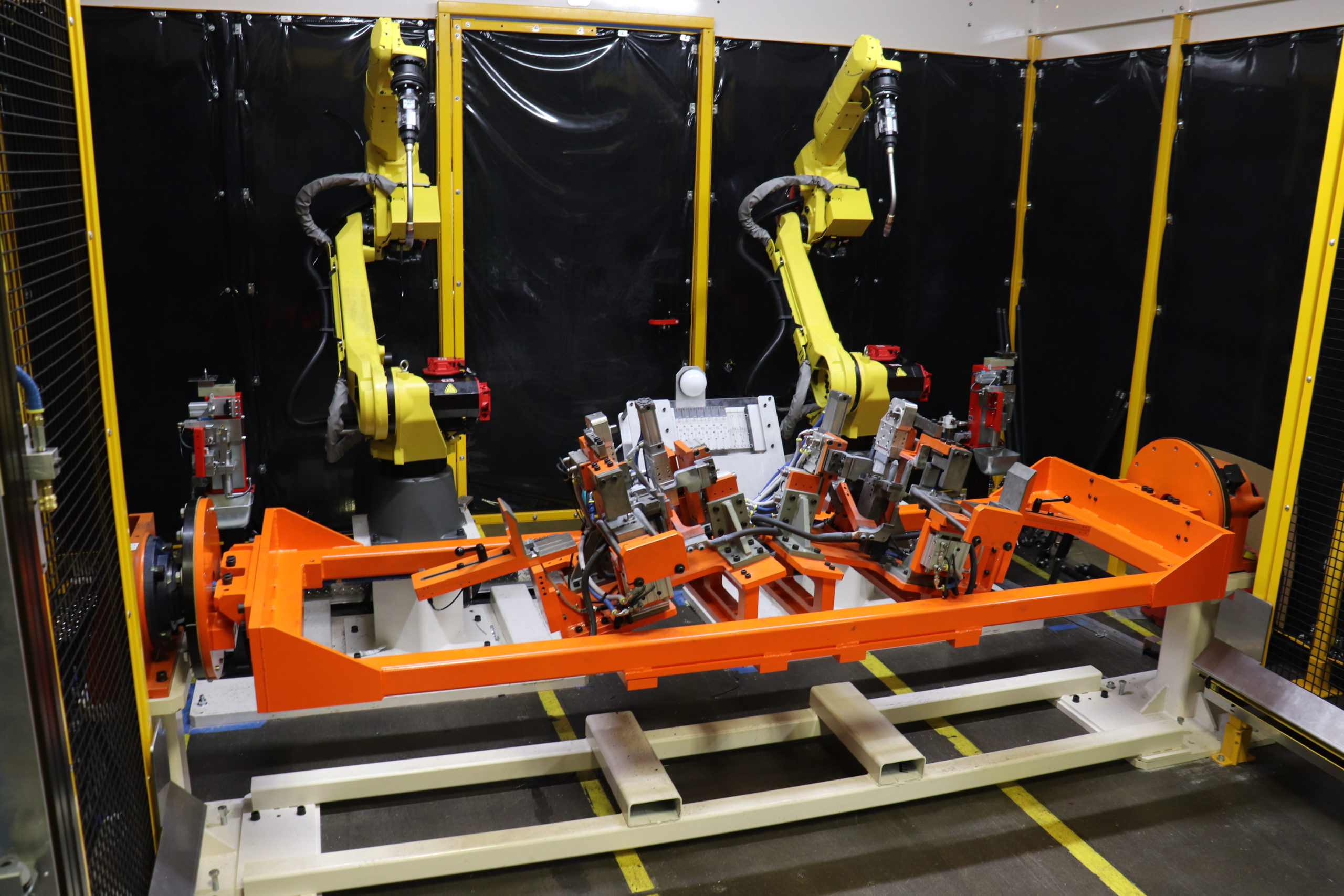
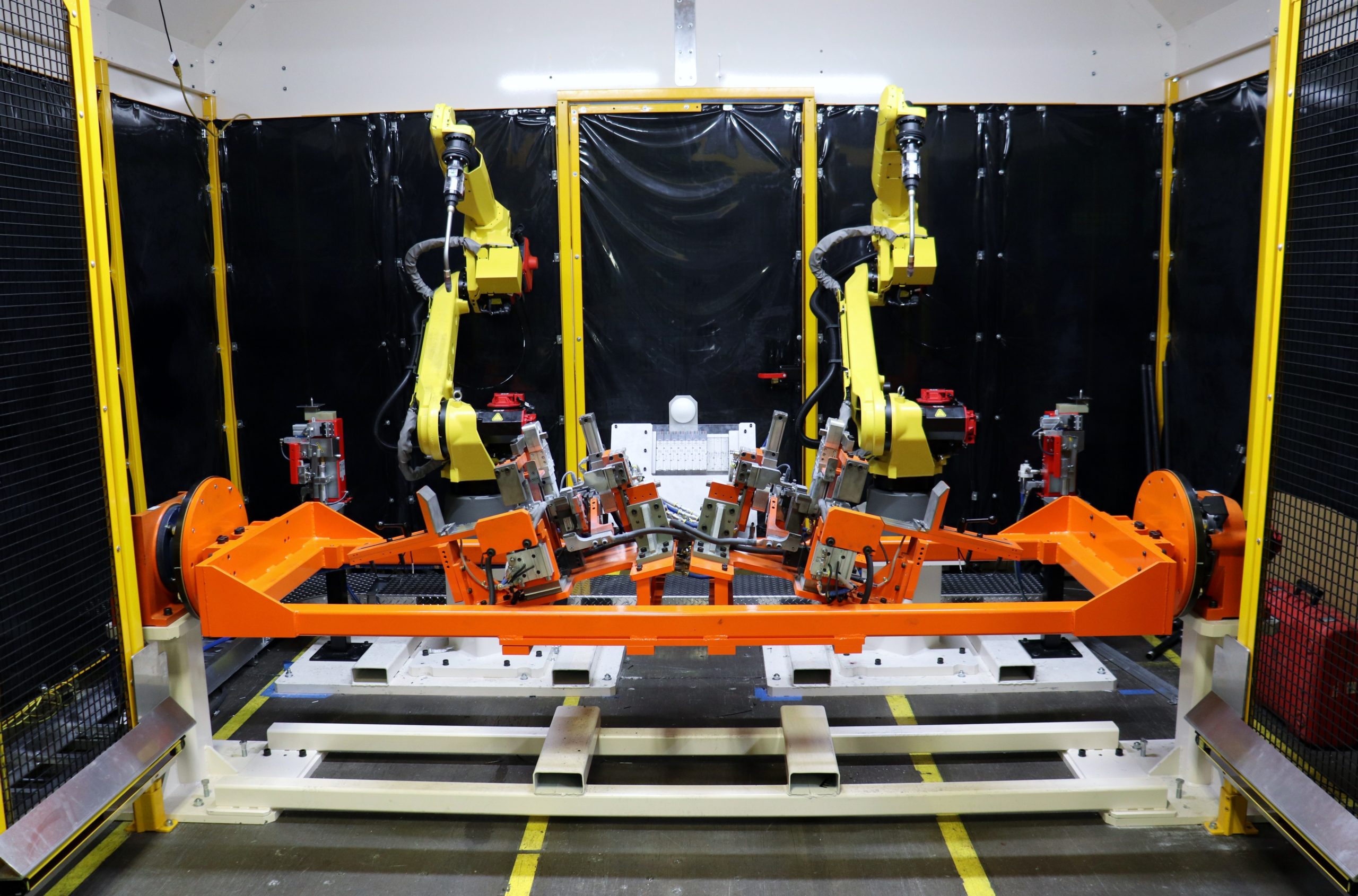
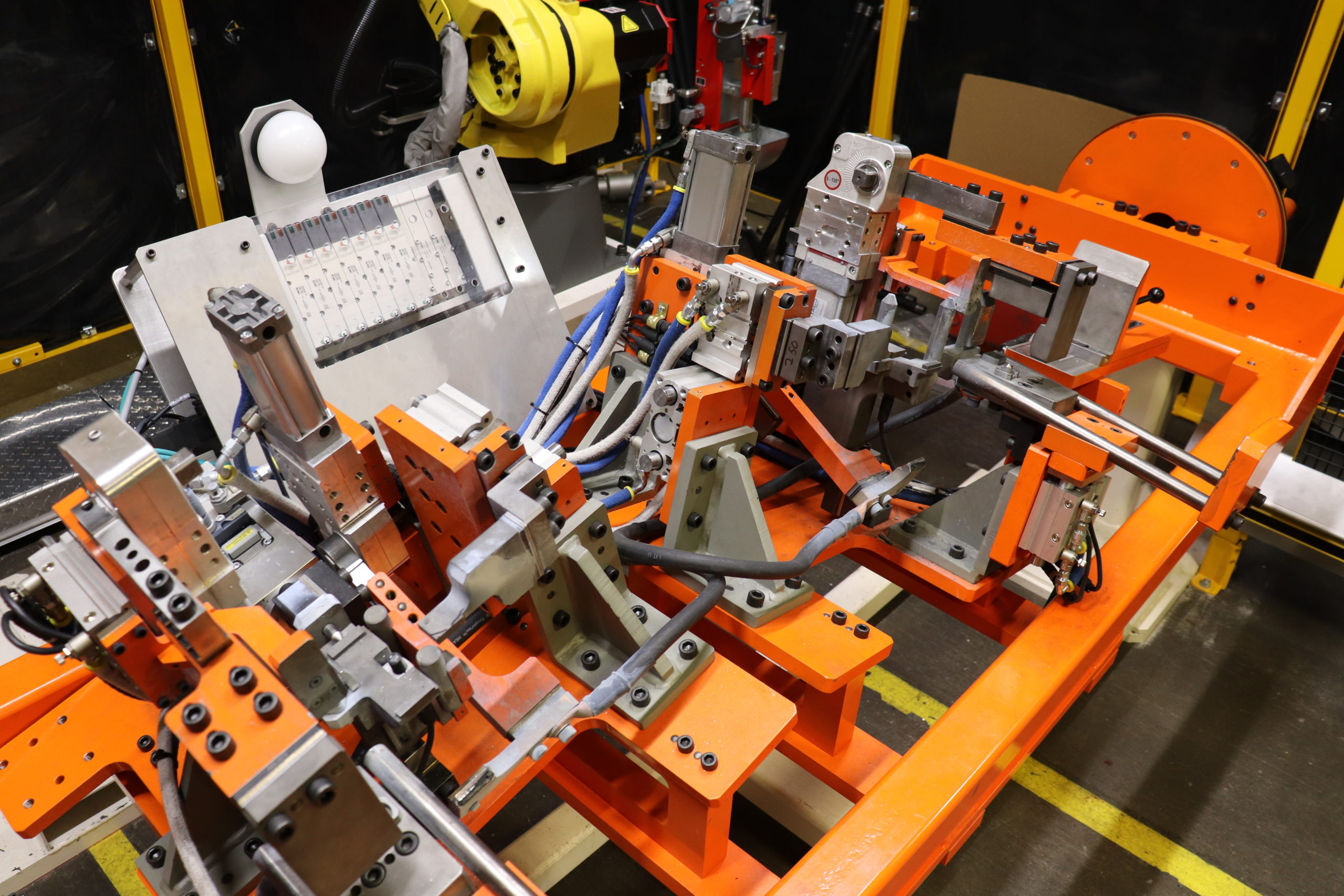
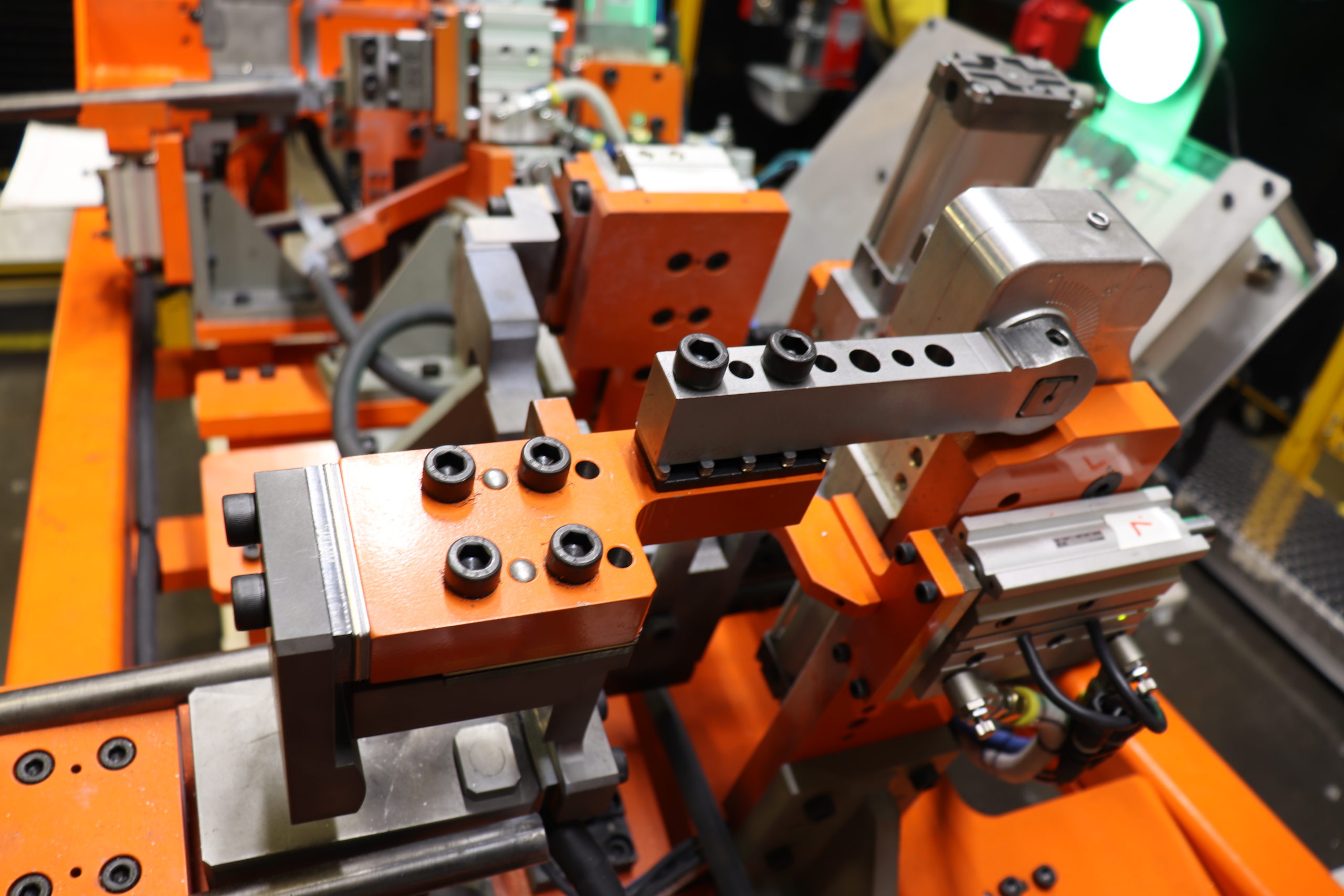
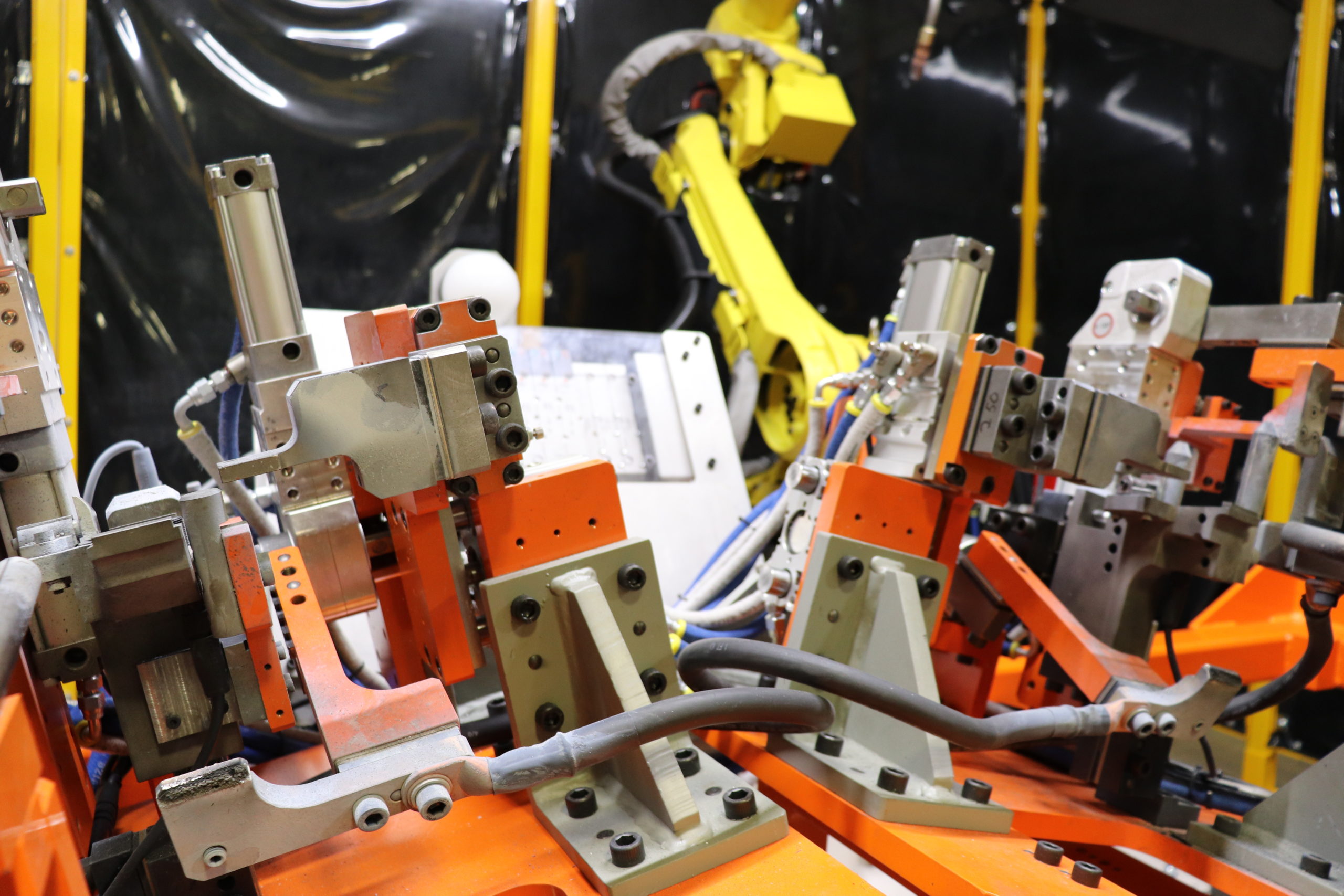
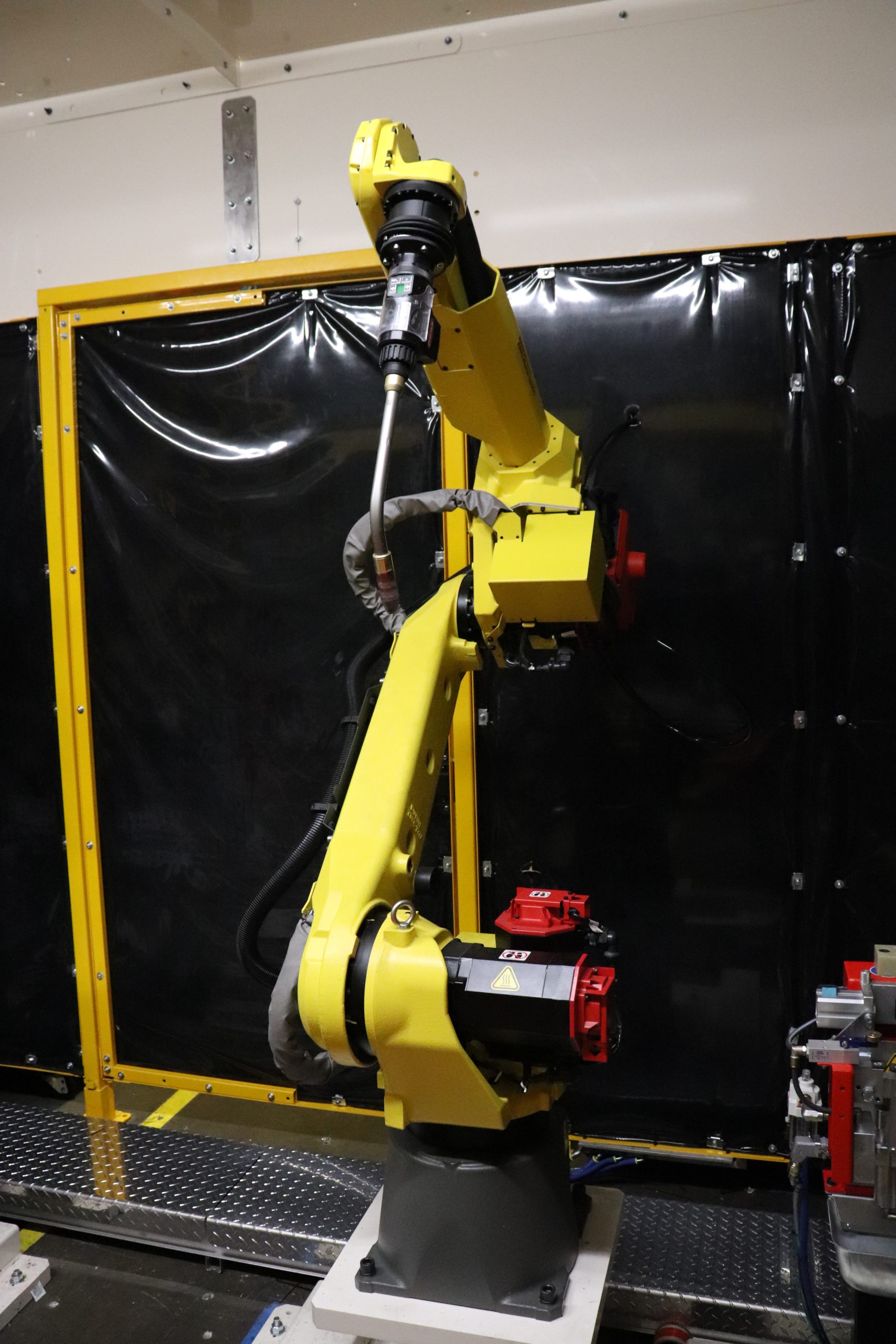
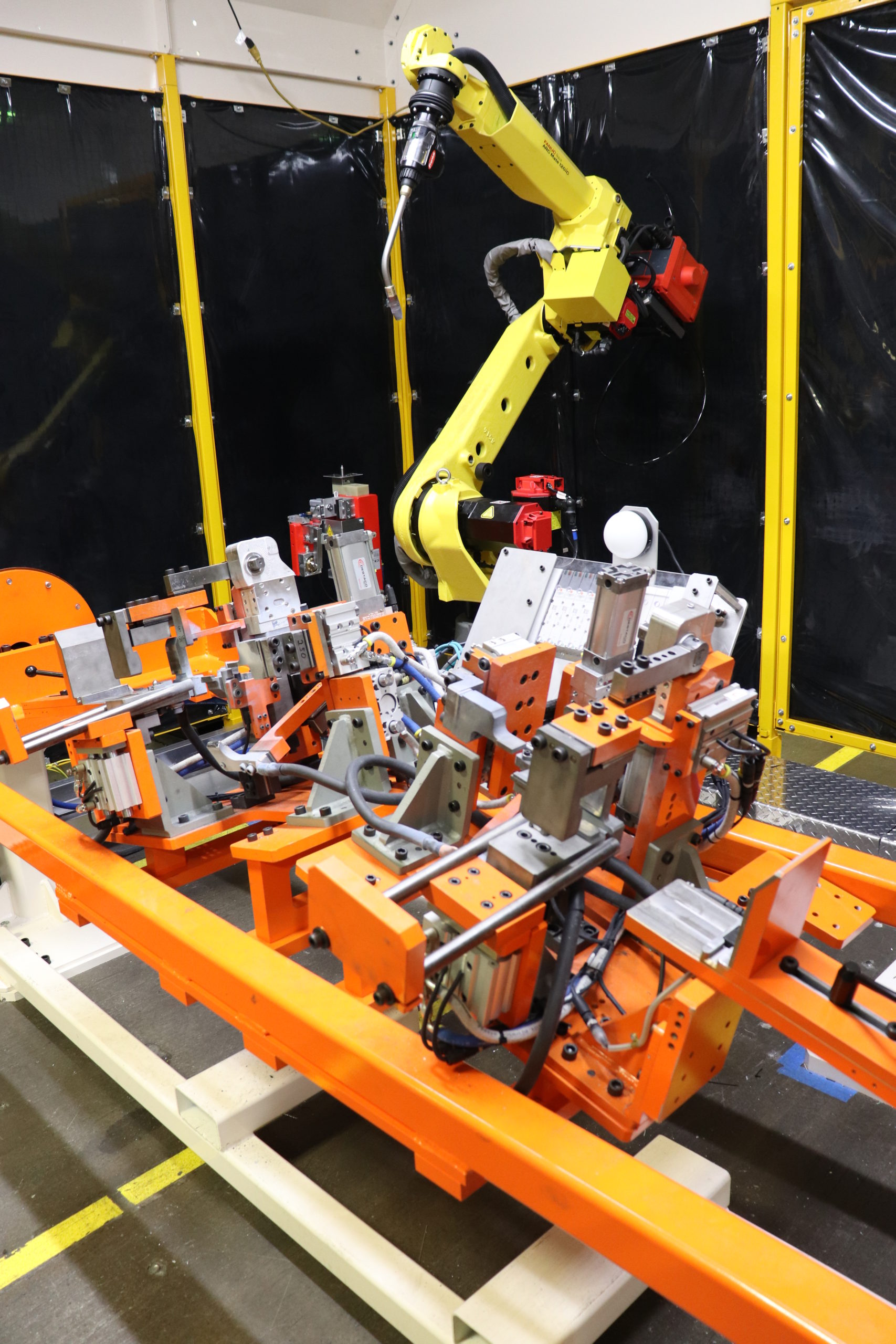
Why Should Companies Use Robotic Welders In Manufacturing?
History of Automated Welding
While Robotic Welding did not come into existence until the mid-20th century, humans since the bronze ages have been crudely welding metal objects together. From pressure lap welding, to hammer welding, crude welding techniques have been known by humans and employed in manufacturing settings. But sadly, for nearly 3,900 years, what was known about metal welding would not change.
But in 1961, under the watchful eye of George Devol and Joseph Engelberger, an automated robotic welder was introduced into a manufacturing process. In a General Motors plant, in Trenton, New Jersey, Mr. Devol and Mr. Engelberger installed a robotic arm to retrieve hot die cast parts too dangerous for humans to handle. With 6 degrees of freedom, digital control, magnetic drum memory, and discrete solid-state control components, this early robotic welding machine performed hazardous and repetitive tasks.
For the next 22 years, Unimation, the company of George Devol and Joseph Engelberger, continued to improve upon their original design and implemented their robots in in printing, welding, and part assembly processes. Their contribution to robotic industry is still widely felt and is understood to be instrumental to the quality and efficiency we now enjoy on manufacturing floors today.
Benefits of Robotic Weld Cells
For most companies, and probably yours, manual welding is the manufacturing process of choice for joining metal parts. But if you are like many modern companies you are feeling the global competitive pressure of efficiency and labor costs. If this situation sounds all too familiar just know you are not alone. With the introduction of CNC mill’s / lathes, and the implementation of factory robots, the manufacturing landscape is continuing to evolve and competitively grow. This fact has led many savvy business owners to consider how to increase their throughput and quality while decreasing total scrap rates.
The general consensus of innovative companies is to automate different processes that are repetitive in nature. Luckily for many, due to technological leaps in robotic technology, automated welding has moved from a novel idea in unique situations to a mass solution seen across multiple markets worldwide. Additionally, with a projected American welder labor shortage of nearly 350,000 workers by the year 2023, many companies are starting to view robotic welding as a viable solution to labor issues plaguing the welding industry.
Companies that choose to make the leap from manual welding to robotic welders can see an immediate improvement in quality, throughput, and consistency. No more do companies have to worry about workers going on vacation or inconsistent welds between operators.
How to Develop a Robotic Welding Machine For Your Company
In what application is a robotic welder a good fit? Where should a company start when considering making the jump from manual welding to a robotic welding machine? Like most things in the manufacturing industry it comes back to the payback period and the project ROI (Return on Investment). How long will it take to make the investment back and what will the overall financial return be over the life of the project. Once the financials are considered, and a robotic weld cell is determined to be a financially feasible solution, the next step is to design the weld cell based on the floor space available.
If you are at this stage this is a good time to contact our team of experts where we can assist and advise you on how to move forward. With our decades of experience we know where potential pitfalls lie and how to prevent common mistakes when setting up new cells. Additionally we can help you to optimize your space by consolidating the weld processes of multiple part numbers into one weld cell. That has greatly helped our customers realize a higher ROI and a shorter payback period by reducing the need to build additional cells. We accomplish this by using a common trunnion, frame, weld cell, but unique part fixtures for different part numbers. Within as little as 30 minutes your team could swap out a weld fixture, change robotic programs, and produce new parts in as little as 30 minutes. With the competitive landscape we all navigate these days’ efficiencies like this save time and money.
Example Weld Cell Specifications
- 335,000 Parts Per Year
- 49 Second Part Cycle Time
- Manufactures Two Different Part Numbers
- Single Axis Trunnion Table
- Two Fanuc Robot Arms