Why Should Companies Use Automated Saws?
Do you need to precisely cut material to length? If you answered yes then an automated saw might be the right piece of equipment for you and your business.
Traditionally, if a piece of material is needed at precise lengths, it is first rough cut from stock, and then it is final machined to length. While this may be a sufficient solution for low volumes, it is not adequate for high volume applications. Using this traditional manufacturing approach two operators are needed: One to rough cut the material to length and then another operator to final machine to a tight tolerance.
Tennessee Tool and Engineering has looked at this manufacturing approach and has developed precise automated saws to reduce manufacturing complexity and decrease manufacturing run times. We proudly boast that our saws, when running automatically, can hold a tolerance of +/- .015”. Because of this our automation engineering team has been able to eliminate a manufacturing process and maximize the effectiveness of our workforce.
How Automated Saws Work
For operation, the automated saws use a magazine feed system. This magazine, which is hopper to load blank sticks of material, is initially filled up by a single operator. Next the operator selects the program that correlates with the desired part length and then the machine feeds material into the saw. Part after part the machine runs fully automated producing tight tolerance parts to length.
From the time that the machine starts auto mode, to the time that it completes cutting the last part, the only responsibility the operator has is emptying the final part tote. This system has allowed many of our customers to utilize a single operator to operate multiple automatic machines that produce different part numbers. This in resulted staff multiplication for our customers and an increase in company revenue
Machine Pictures
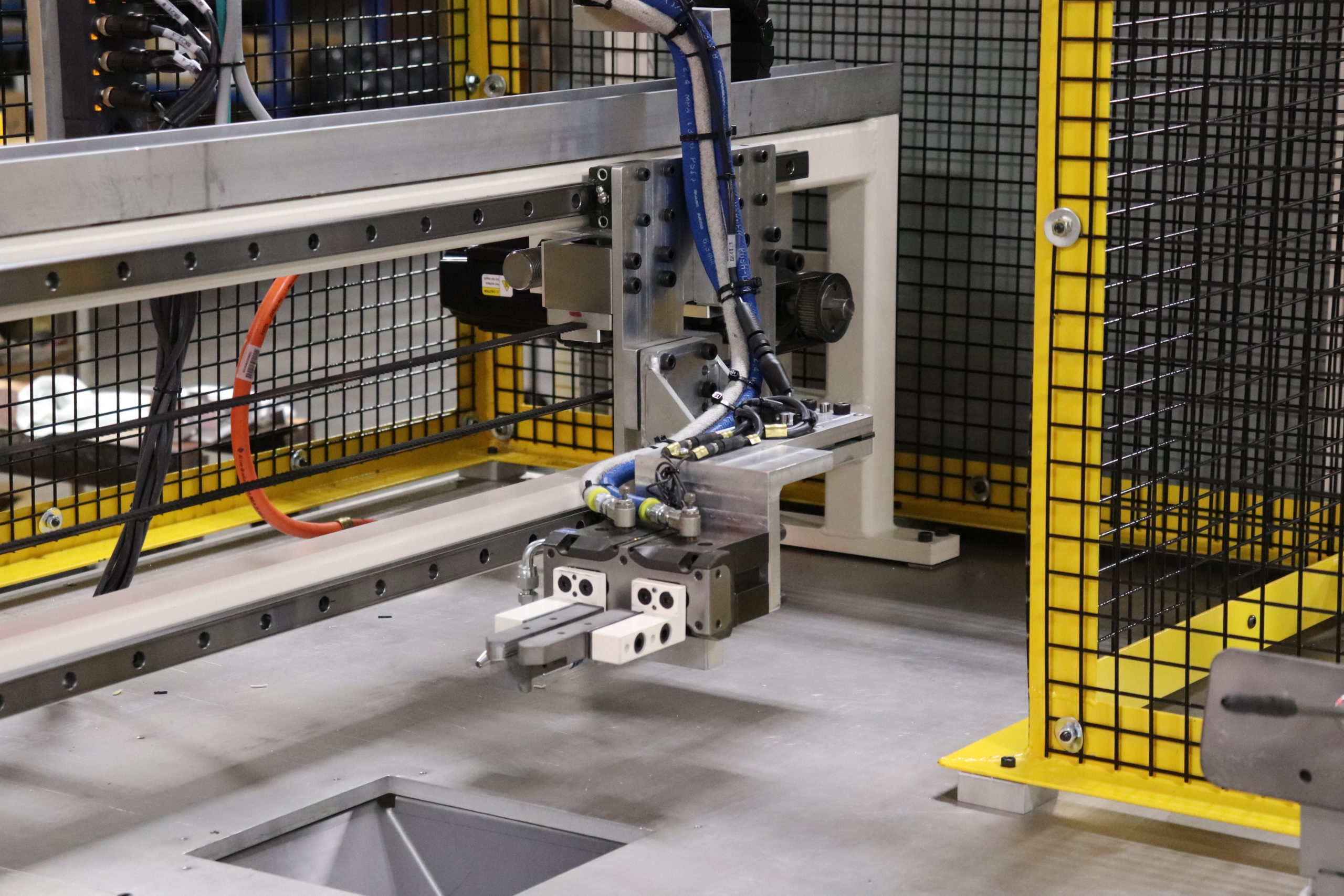
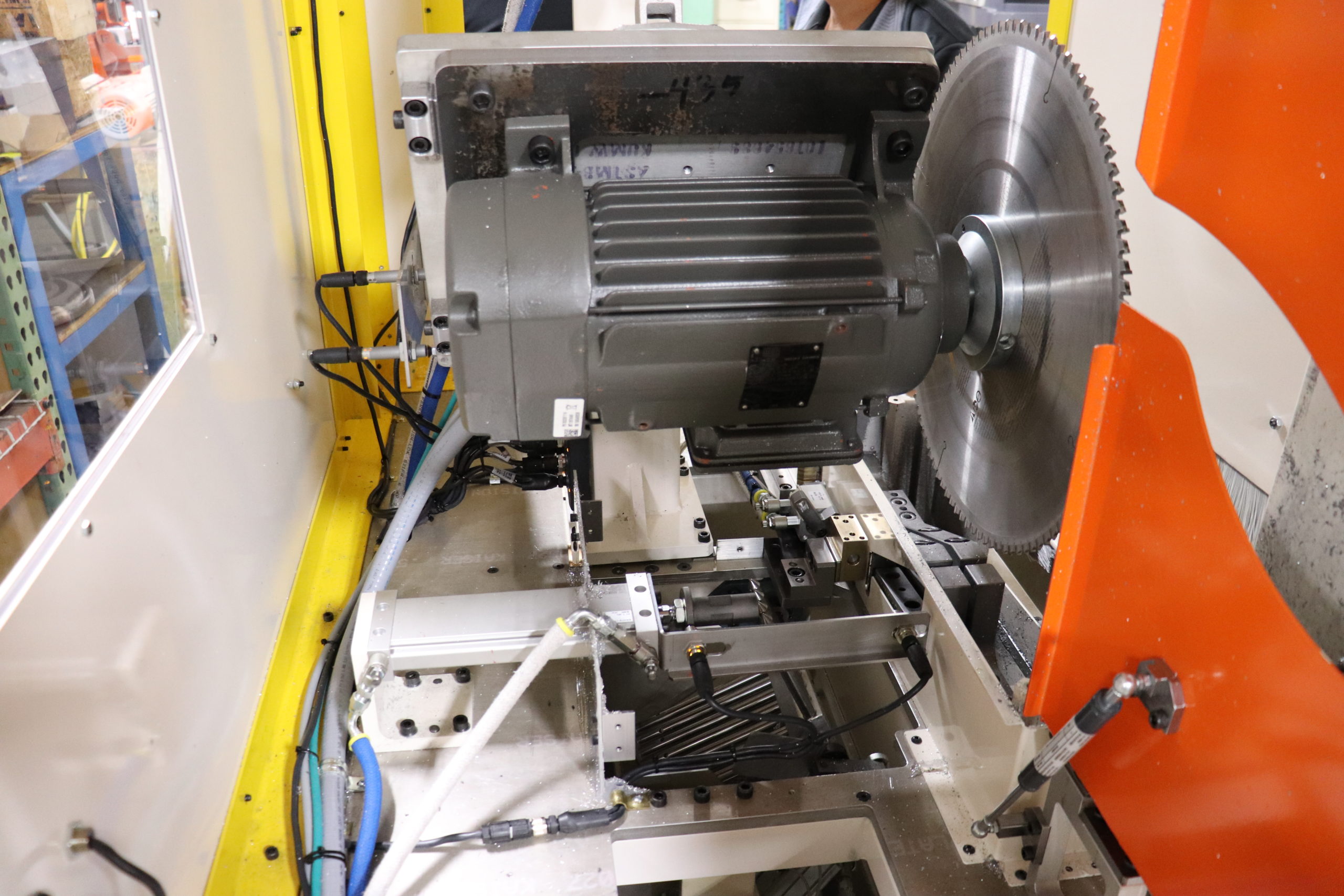
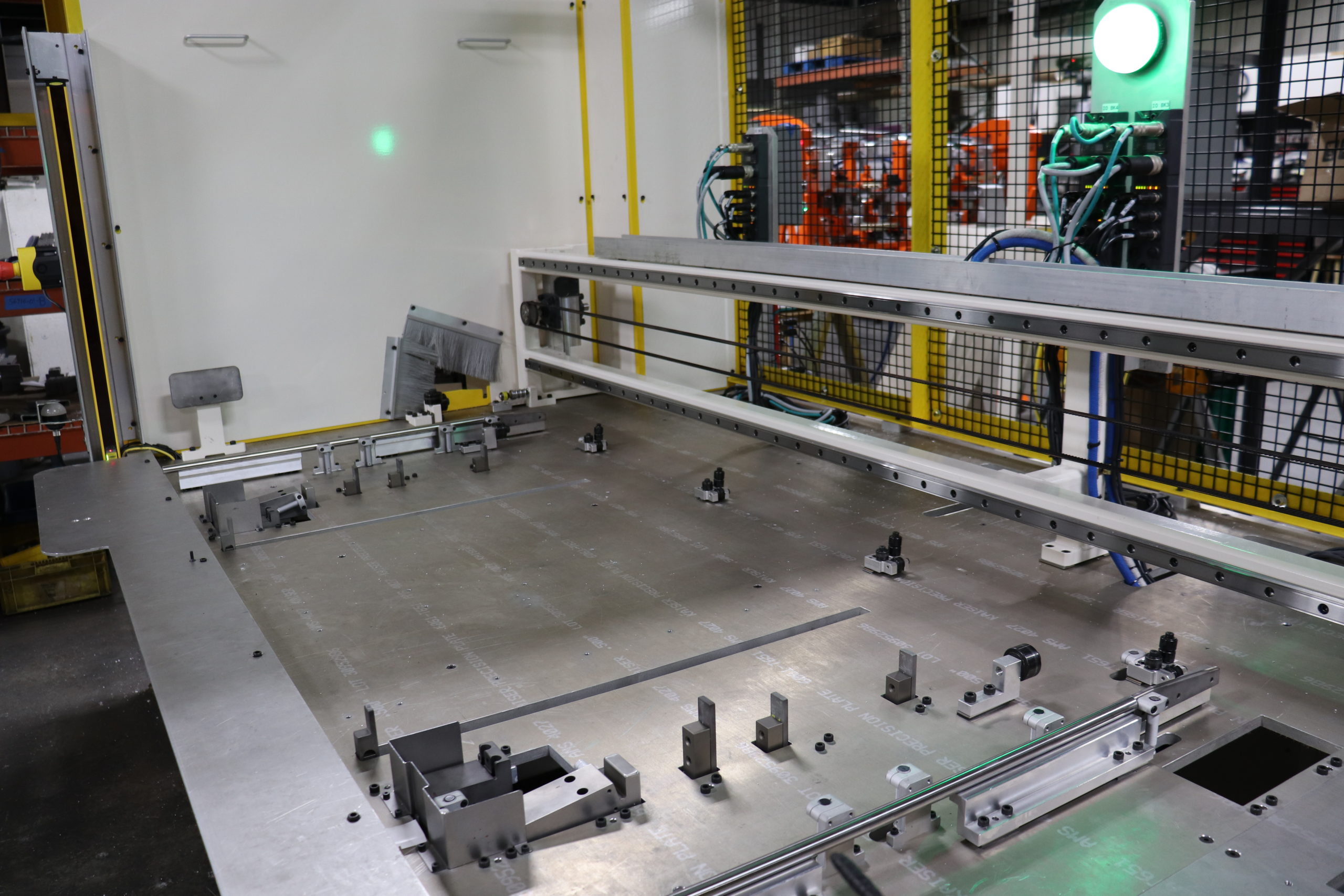
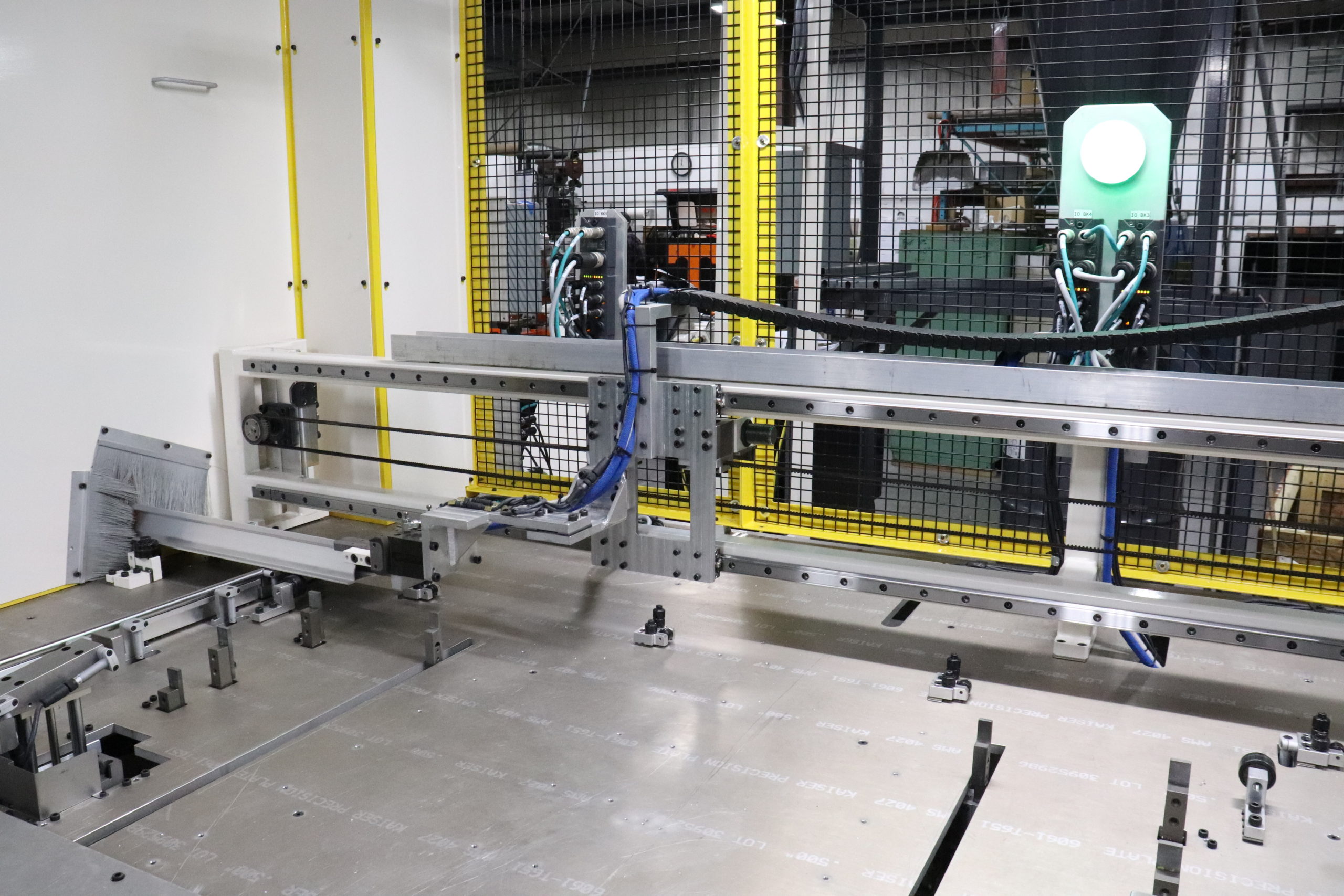
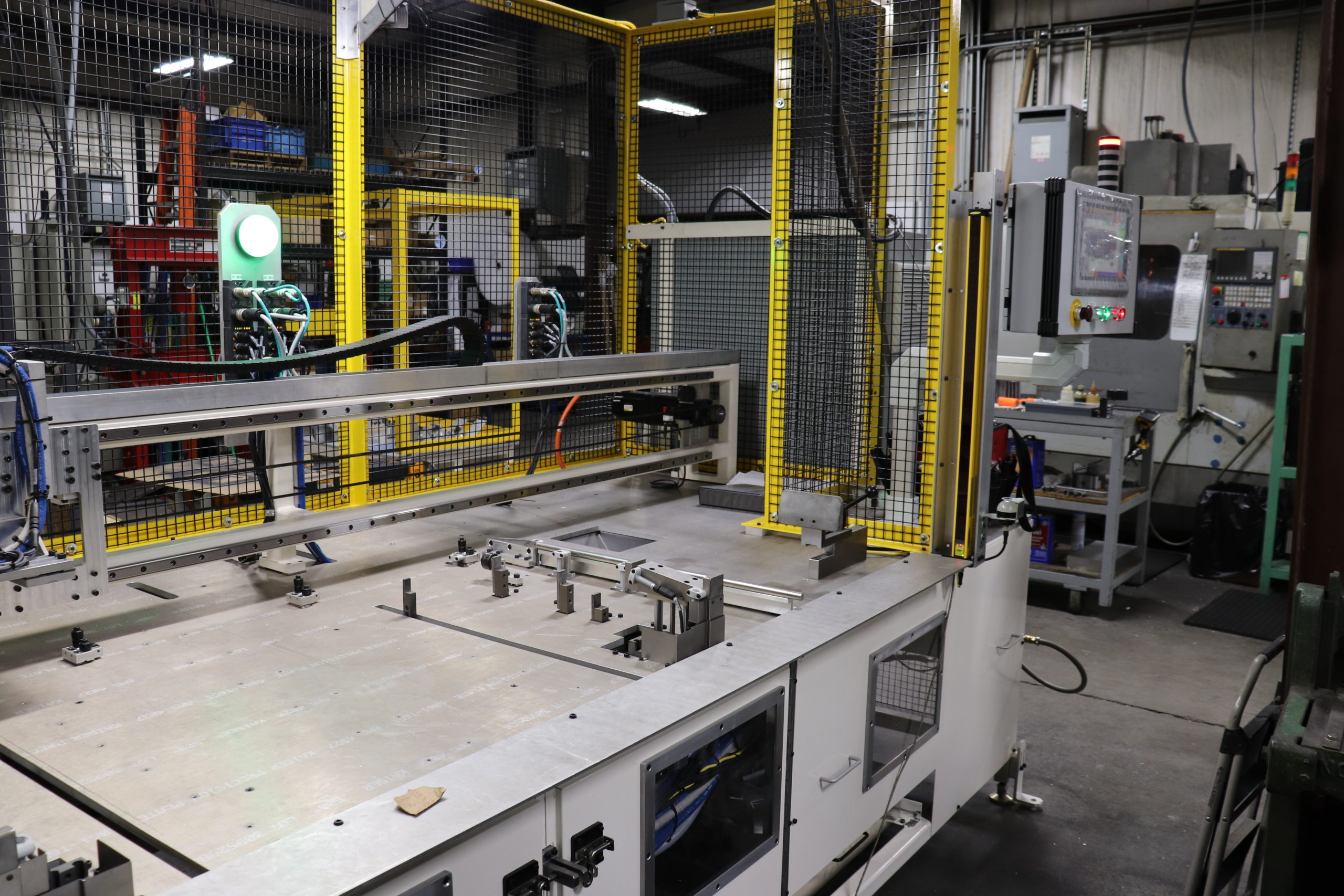
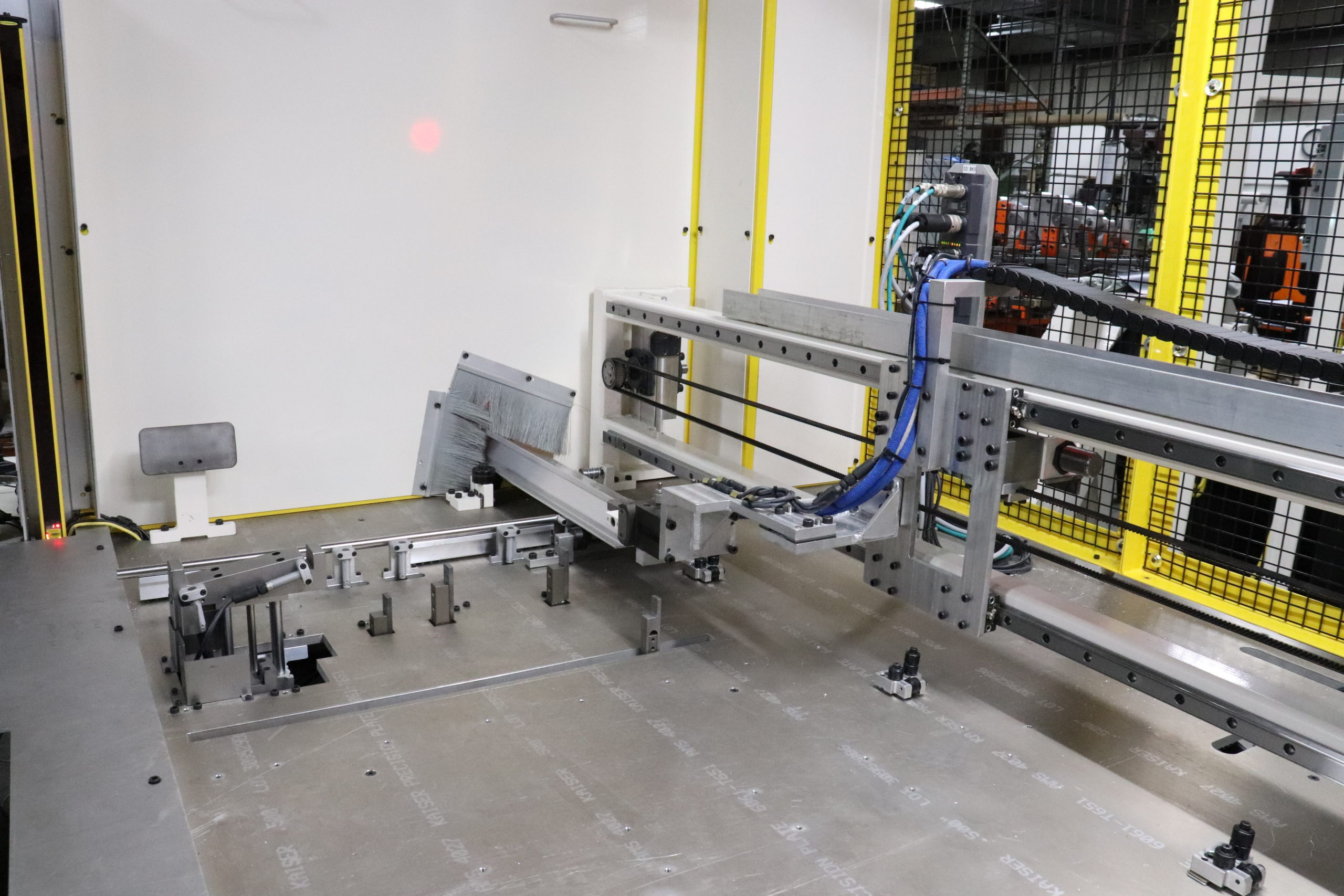
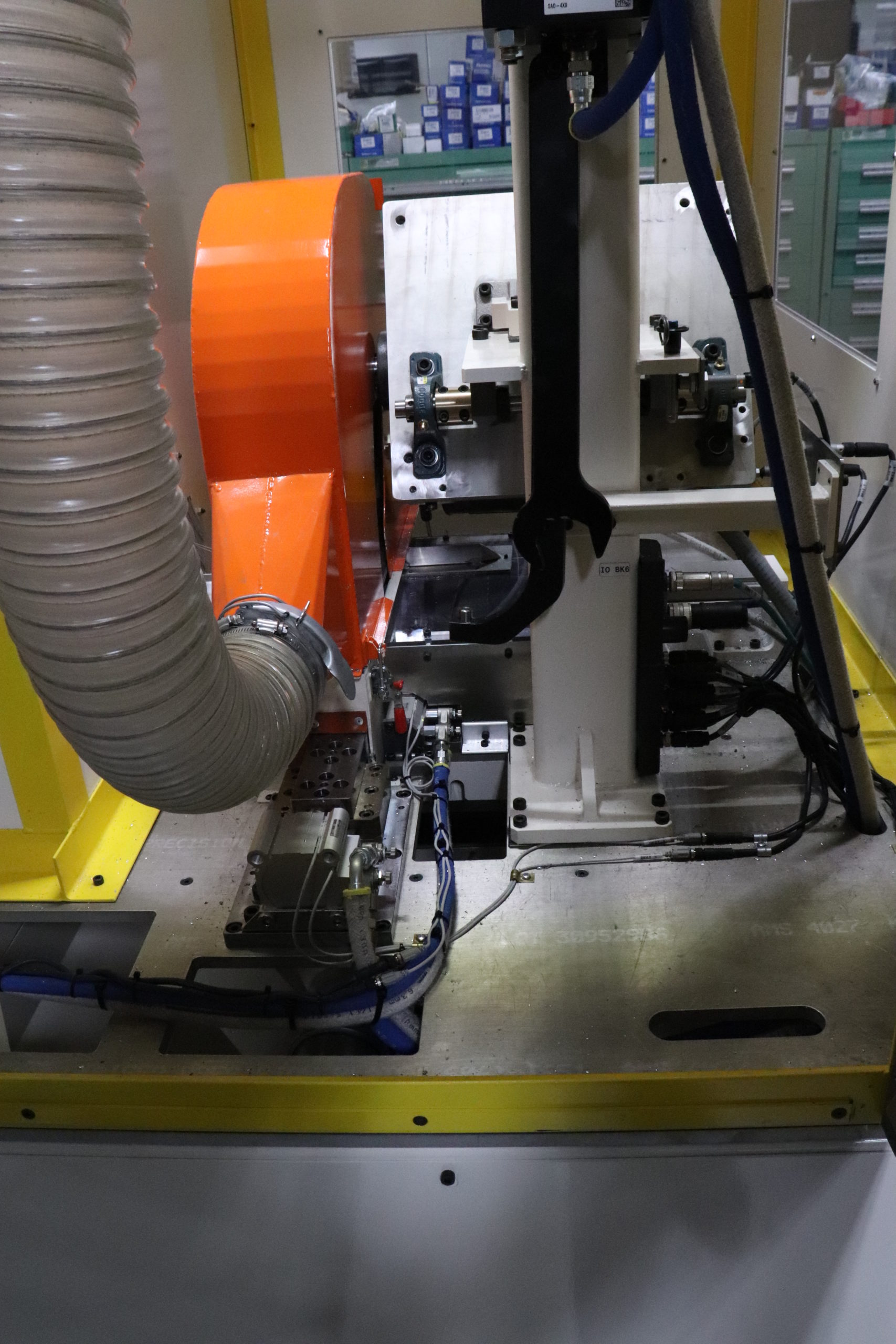
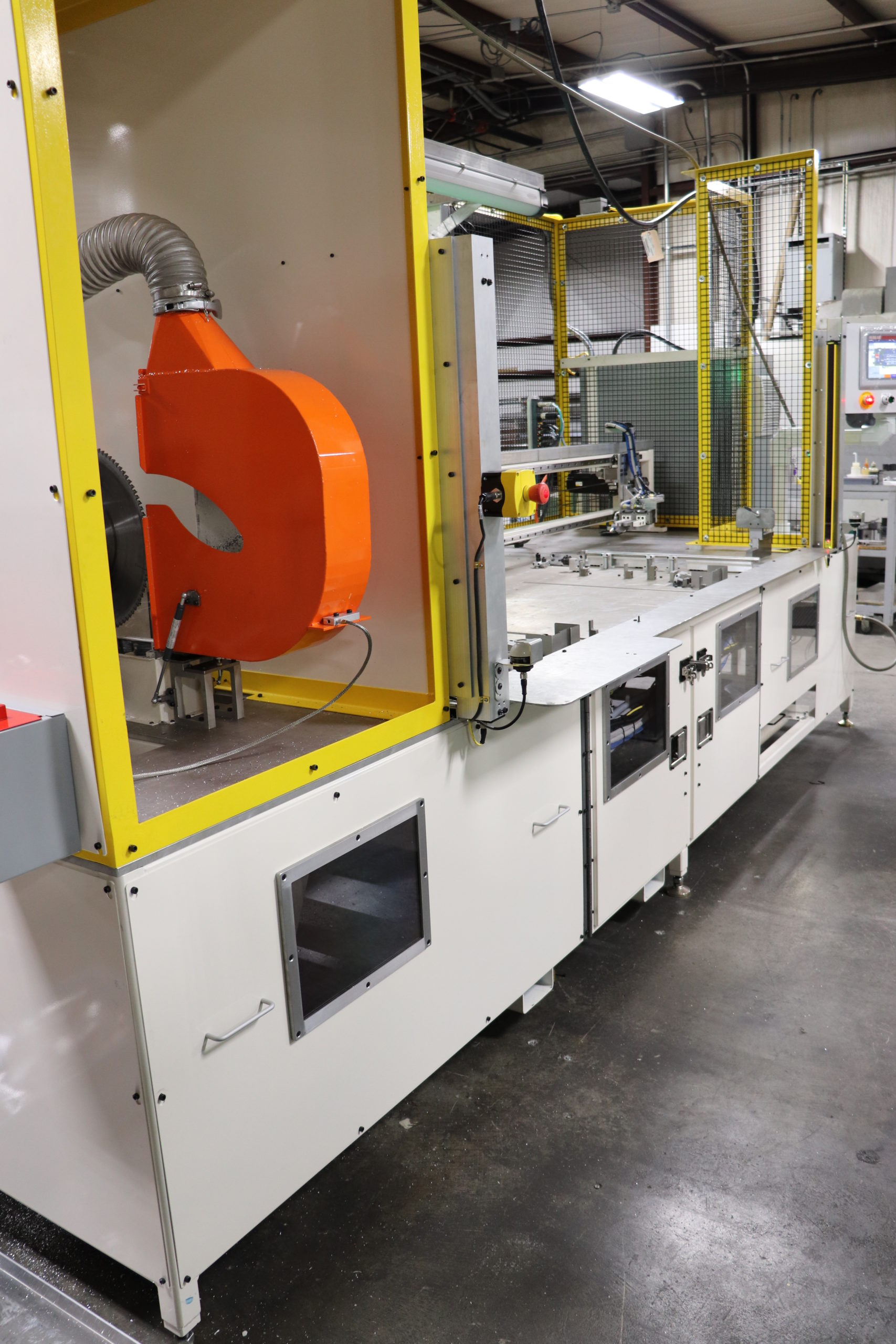
About This Featured Automated Saw Machine
TTE was originally contacted to solve a manufacturing issue a part supplier was having. The customer was needing to speed up a sizing operation on blank extruded aluminum profiles, save floor space, and reduce operator hands on time. The customer required that whatever machine was developed it had to be able to size two different aluminum extrusions profiles. In the end, this machine was to be part of a full line of machines that would cut, pierce and weld the blank extruded aluminum parts to a larger assembly.
Based on the decades of experience TTE felt comfortable with the challenge and developed a fully automated saw cell for the customer. The machine would receive blank aluminum extrusion profiles, auto feed them into the saw, and cut them repeatedly to precise lengths.
Machine Specifications
- 670,000 Parts Per Year
- 24 Second Part Cycle Time
- 35 Minute Uninterrupted Run Time
- Produces 2 Different Part Numbers Using 2 Different Extrusion Profiles
- Dust Collection System to Remove Saw Chips
- Simple In Operation
Related Machinery